“water , water everywhere an not a drop to drink”…thats the problem with spending time on the ocean. Salt water is plentiful but not of much use to supporting a crew aboard a boat. That’s where a water maker is the indispensable bit of kit if one intends to spend any real time on the ocean. “Caprice” can hold 650 litres of fresh water. Surprising how quickly one can go through all that water. So our water maker is precious and in constant use. However, as we approached Bonifacio we noted that the water maker was struggling to give us anything more than a few litres before the “poor quality” light would indicate that no more water was forthcoming and we would have to go into conservation mode.
We had called the manufacturer and ordered new membranes for the device and settling into a relaxed pace in Bonifacio as we waited for the parts arrive. It took 4 days for the membranes to show up at the marina office and I was quick to get into action. Even with a good working understanding of the water maker it took 3 hours to disassemble the membranes tubes and various plugs and seals to allow access tot he failed membranes.
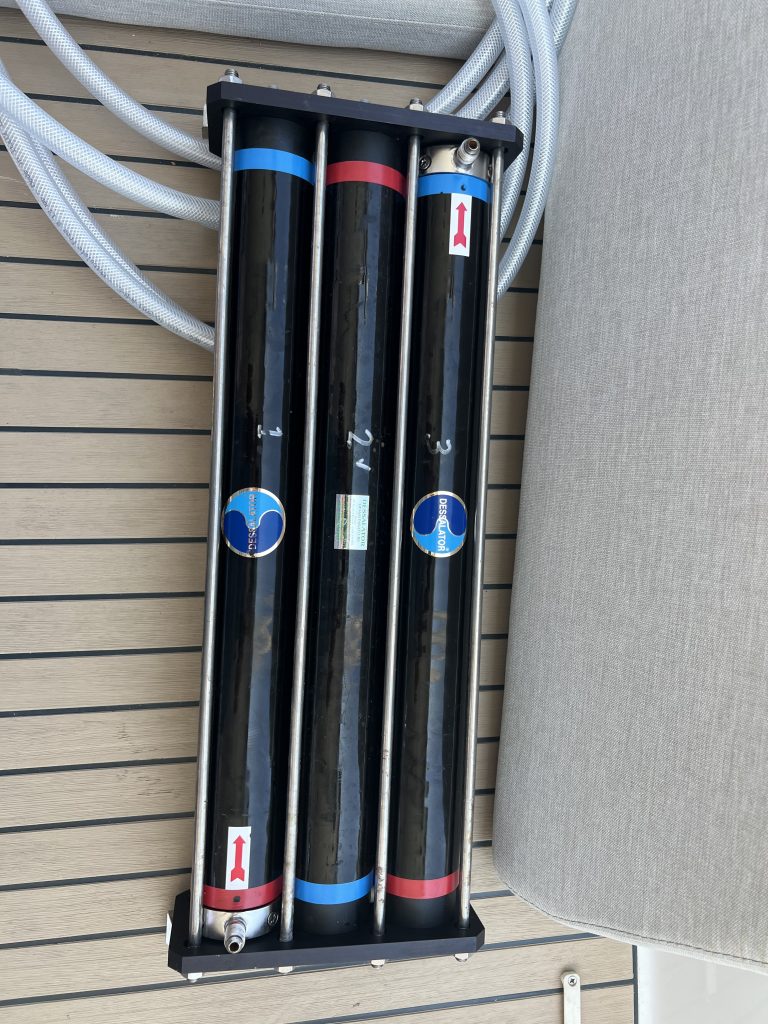
The disassembly was tricky and not easy. I managed to connect a water hose to the membrane tube inlet and with a dozen hard hammer blows to the plug ends I manage the drift the end plugs off the tubes.
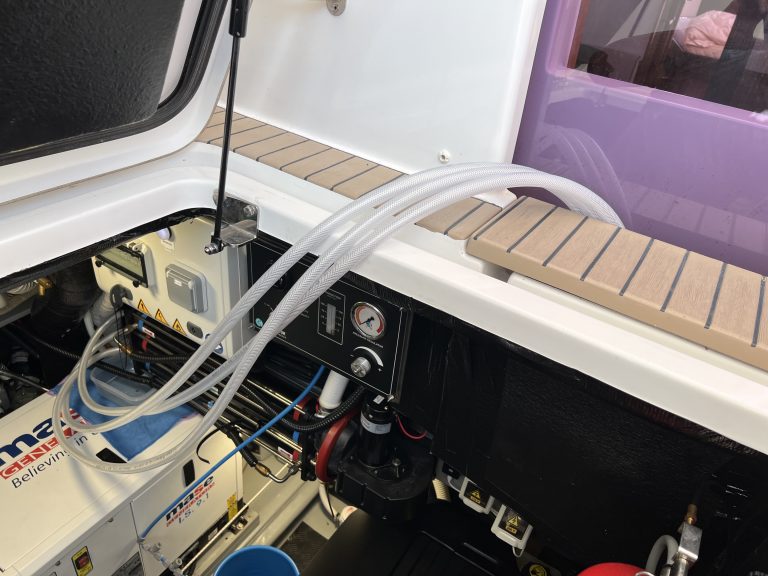
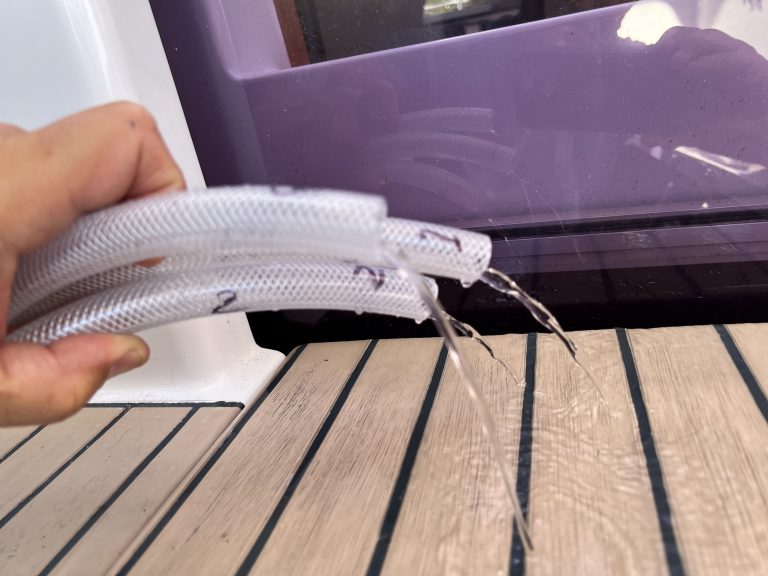
Only two of the 3 membranes were defective so I was spared having to struggle with the last one. Re-assembly was tricky since the seals made a point of catching up on the rim of the membranes tubes and defying all attempts to hammer the end plugs home. Fiddling with a plate head screw driver, poking, prodding, and swearing produced two tubes loaded with the new membranes.
The reassembled block of 3 membranes was re-installed in the boat and the system was put through a pressure test. Of course, this failed and water dribbling through several of the seals meant dismounting the membranes assembly and another hour of swearing, poking, and prodding with a few choice hammer blows to get all the respective parts back together and in to the engine room mount.
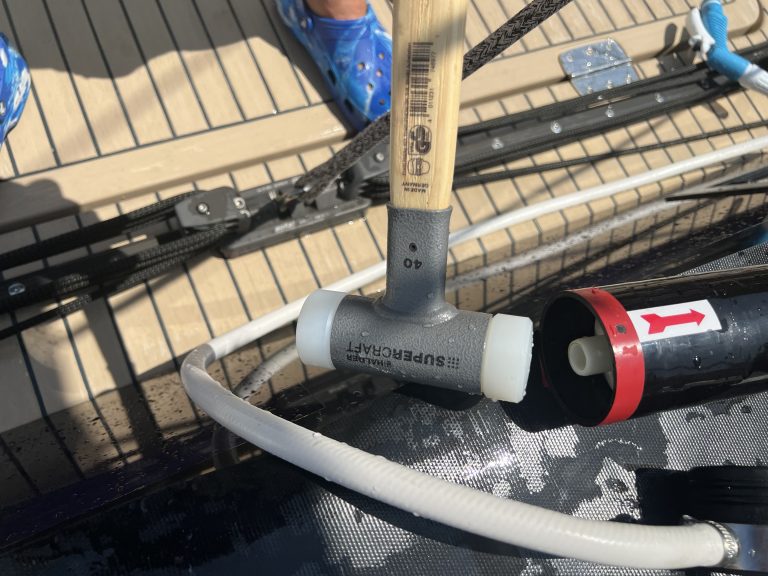
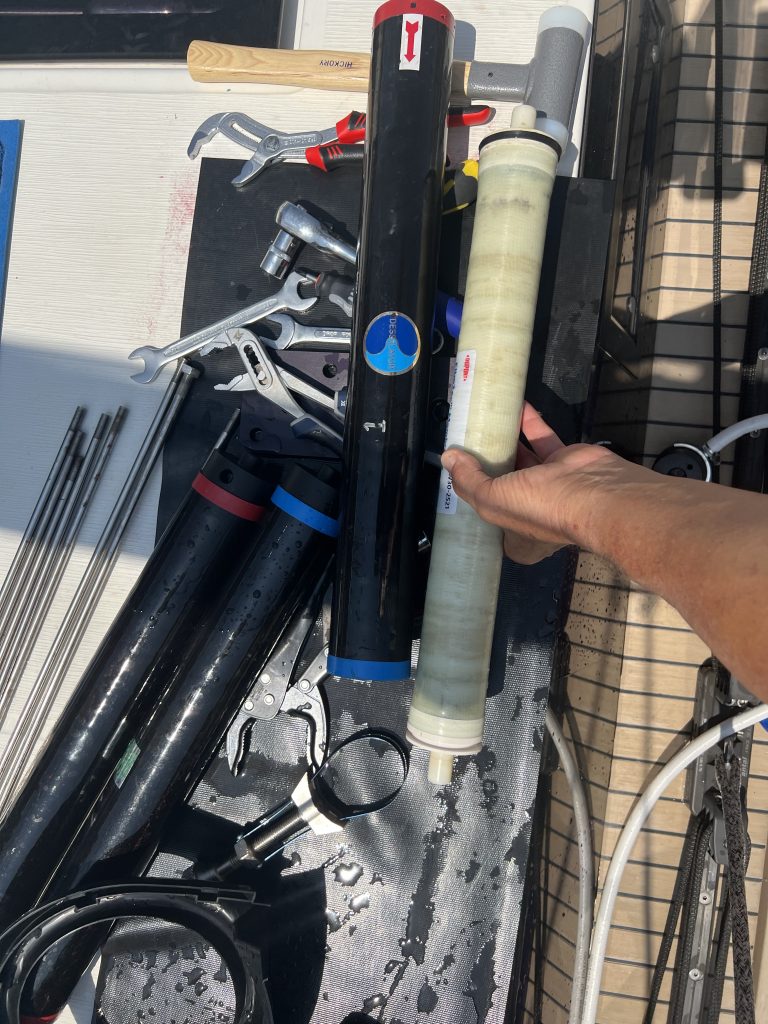

After another bit of testing the water quality with my makeshift test-tubes indicated that we finally has “good” quality water and I breathed a sigh of relief.